If you are looking for competitively priced, high-precision industrial sensors that will improve your operations, the team at Applied Industrial Controls, Inc. has got you covered. Whether you're leaning toward an analog sensor, digital sensor, or need a sensor that will stand up to a hazardous environment, you can count on us to get you what you need. Get in touch with us today to learn more.
What Should I Consider
When Choosing a Sensor?
Do I Need an Analog
vs. Digital Sensor?
Should I Choose a 0-10V vs.
4-20mA Analog Signal Sensor?
How Should I Choose a Hazardous Environment Sensor?
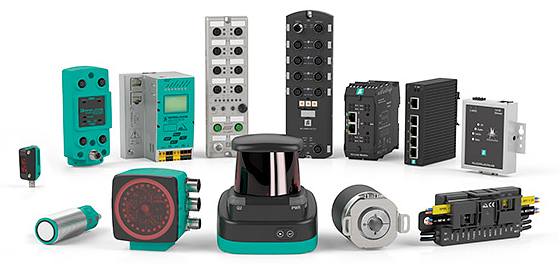
What Should I Consider When Choosing a Sensor?
There are many types of sensors available that can provide various types of information. When considering an industrial sensor, make sure you carefully review all styles available. There are proximity, photoelectric, positioning, vibration, pressure, temperature, flow, and level sensors, to name a few. When choosing a sensor, first of all, you must have ample knowledge about the application and operational requirements. This will help with making the best choice of sensor for your specific needs. Next, it's important to understand the capabilities of the different types of sensors. Finally, it is critical to test the sensor with the piece of machinery it will be installed on to ensure it performs as needed. Some of the operational requirements needed when choosing a sensor:- Temperature Range
- Protection Class
- Input Voltage / Supply Power
- Type of output signal (Voltage, Amperage, or dry contact)
- Physical Size
- Response Speed
- Repetition Accuracy (hysteresis)
- Mounting Type
- Sensing Range
Do I Need Analog Industrial Sensors or Digital Industrial Sensors?
Sensors provide information from signals. Machinery and devices pass signals between them to send and receive information. Signals can be transmitted through wires (electrical) or air (radio frequency waves).
Analog signals are continuously changing with respect to time and can have an infinite number of values. Examples include voltage, current, pressure, flow, and sound. These signals are always slightly changing or variable. If it is necessary to document a specific value at a certain time, an analog sensor will give that value. Digital signals only have two values as opposed to an infinite number. These values are usually high and low limits or "on and off." The previously mentioned examples of voltage, current, pressure, flow, and sound can also use a digital signal. A pressure switch is an example of a digital sensor. If a pressure sensor is set to activate once a signal reaches the high limit, it may open a dry contact when the pressure rises above the set value. This type of limit sensor is often referred to as a switch.
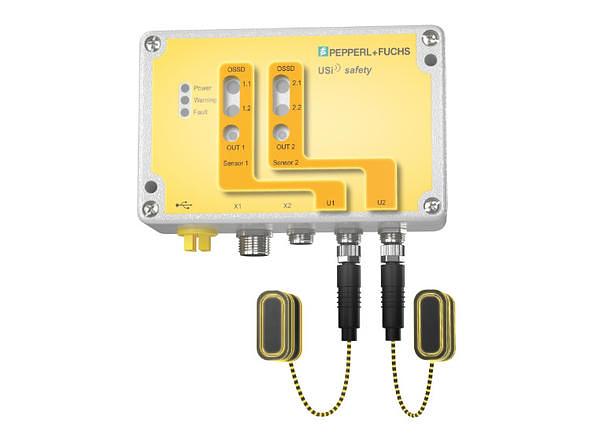
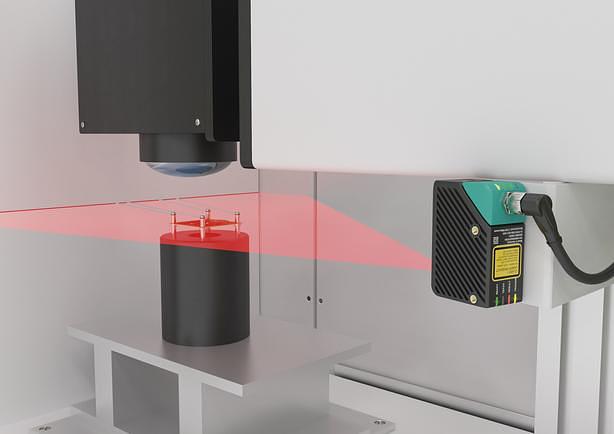
Should I Choose a 0-10V vs. 4-20mA Analog Signal Sensor?
When choosing an analog signal sensor, the most common are 0-10V, 0-5V voltage sensors, and 4-20mA current sensors. Just about every industrial controller in the marketplace will accept a 0-10V sensor signal. This type of signal is very common and easy to troubleshoot. The sensor output can be measured and read quickly with a Digital Multi-Meter or Voltmeter, which are common tools used by operators and maintenance personnel. A downside to this signal is that other electrical devices can induce voltages onto the signal lines that can deteriorate the original 0-10V signal. Also, over longer wire lengths, wire resistance can cause a voltage drop of the 0-10V signal.
A 4-20mA signal sensor provides greater protection against electrical interference and signal loss over longer wire lengths. At the lowest value of a 4-20mA signal, the signal remains active because 4mA is used as the zero condition. When you see 0mA, you know there is an open circuit or cut wire, and an automated alarm can be activated directly from the PLC. However, with a voltage output, 0V is a valid output for the zero condition. Most newer industrial controllers will accept the 4-20mA current signal.
What Should I Consider When Choosing Industrial Sensors for Monitoring in a Hazardous Environment?
Sensors are important for equipment operating in hazardous environments, and if they fail, they are ineffective for monitoring operations. Hazardous environments include damp or humid conditions, areas with extreme temperature fluctuations, electrostatic discharge potentials, areas with vibrations, and conditions where particulates have access to enter the equipment.
When selecting a sensor, you must consider the environmental hazards that the sensor will be exposed to and choose a sensor that is best suited to handle those specific hazards.
If you would like more information about our services or want to integrate your sensor into a custom control system, get in touch with Applied Industrial Controls, Inc.
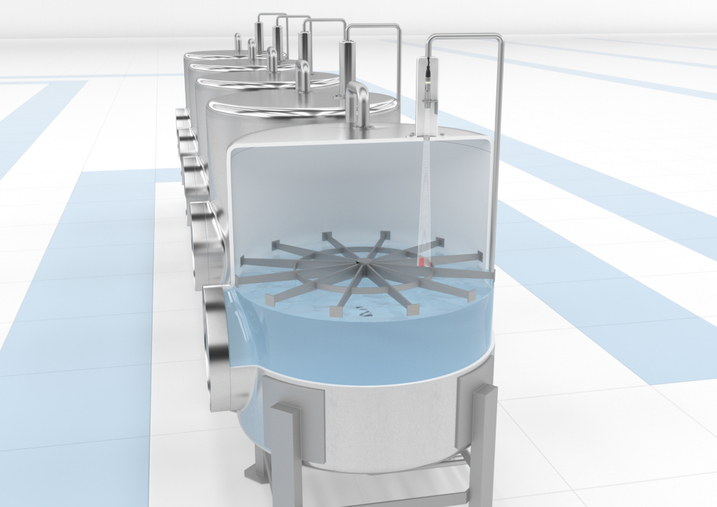
MANUFACTURERS CERTIFICATIONS
