Are you curious about how you can get your system devices and machines to talk to one another efficiently and in real-time? Are you struggling to find ways to collect data for your IIoT applications? Effective automation relies on multiple devices talking to each other through communications protocols. And smart devices communicating with one another effectively and efficiently can reduce labor costs and production time. The industrial communications experts at Applied Industrial Controls, Inc. can help make this happen for your operations systems.
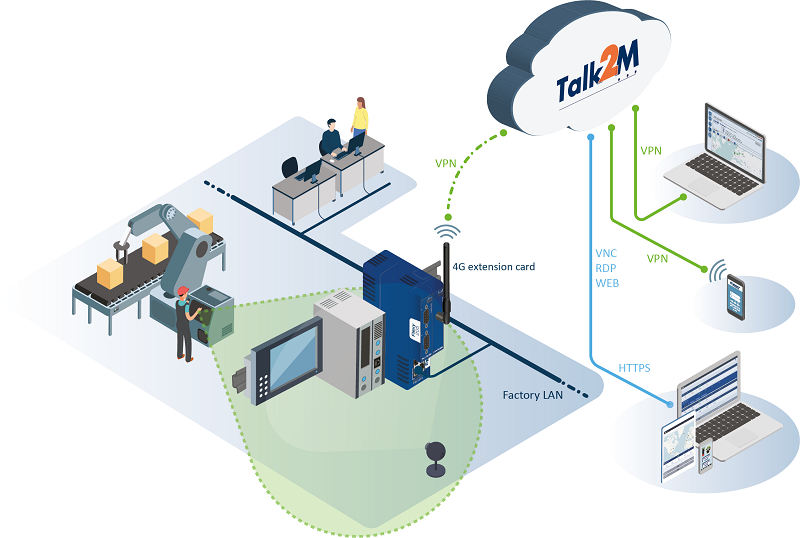
What Is an Industrial Communication System/Network?
An industrial communication network is a means for automated mechanical equipment and devices to communicate with each other and with humans who operate the system controls. These networks can transfer massive amounts of real-time data from large industrial operations systems, even in harsh environments. They can also control what data is stored or presented. Data communication occurs from transmitters to receivers through a cable connecting them. Communication can be achieved between devices such as HMIs, PLCs, VFDs, sensors, data loggers, computers, IPCs, and other electronic devices throughout the system. Industrial communication networks can also connect with SCADA systems which are utilized for IIoT data collection.What Types of Industrial Communications Protocols Should I Consider?
There are many choices for industrial communication networks. Some of the most common are:
- Profinet / Profibus
- Modbus
- Ethernet IP
- Modbus RTU
- Modbus TCP
- Modbus Serial (RS232 or RS485)
- MQTT
- MTConnect
- Canbus
- Bacnet
- ControlNet
- DeviceNet
Each network has different protocols or rules used for communication between electronic devices, and there are important things to consider when choosing the best network for an automation system. First, the speed and control of data collection and transfer are some things to consider. Next, determine whether programmed functions or configured functions are preferred. A third deciding factor is, are there built-in network device diagnostics. Another important thing to consider is the types and availability of product support. A few more factors are the range of applications that the network can manage, plans for system expansion, data form compatibility, and manufacturer’s conformance requirements can all influence the decision.
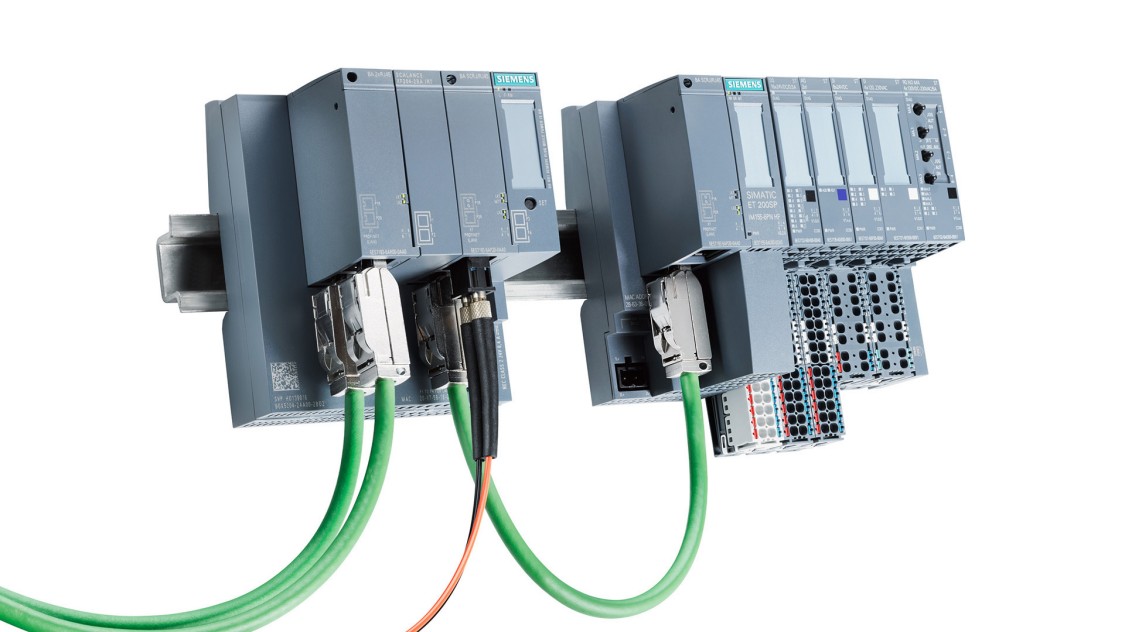
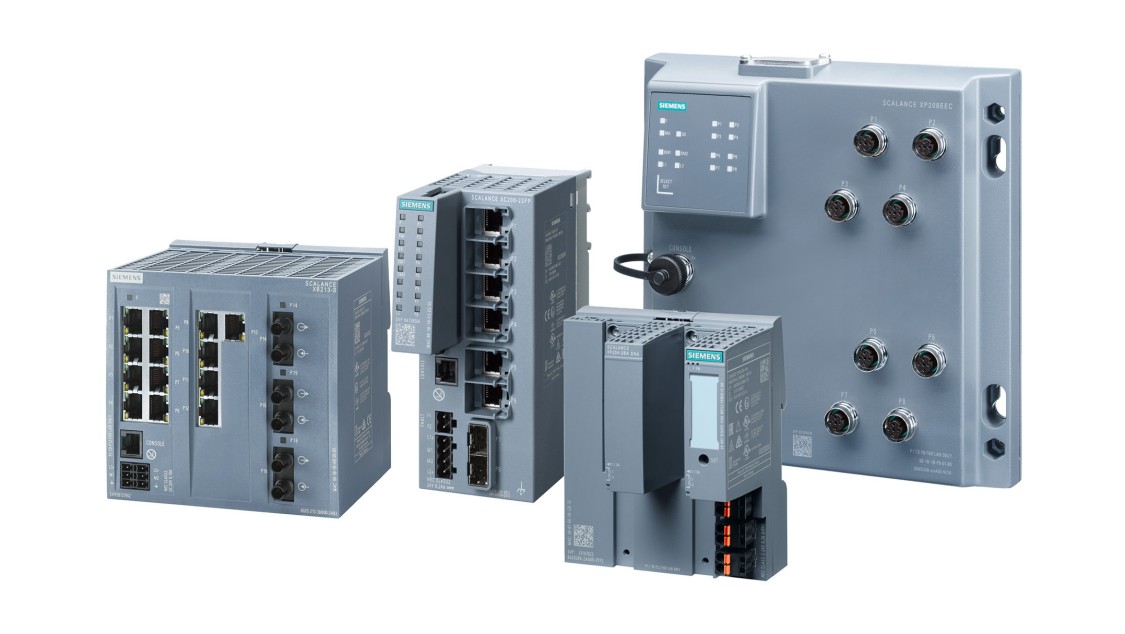
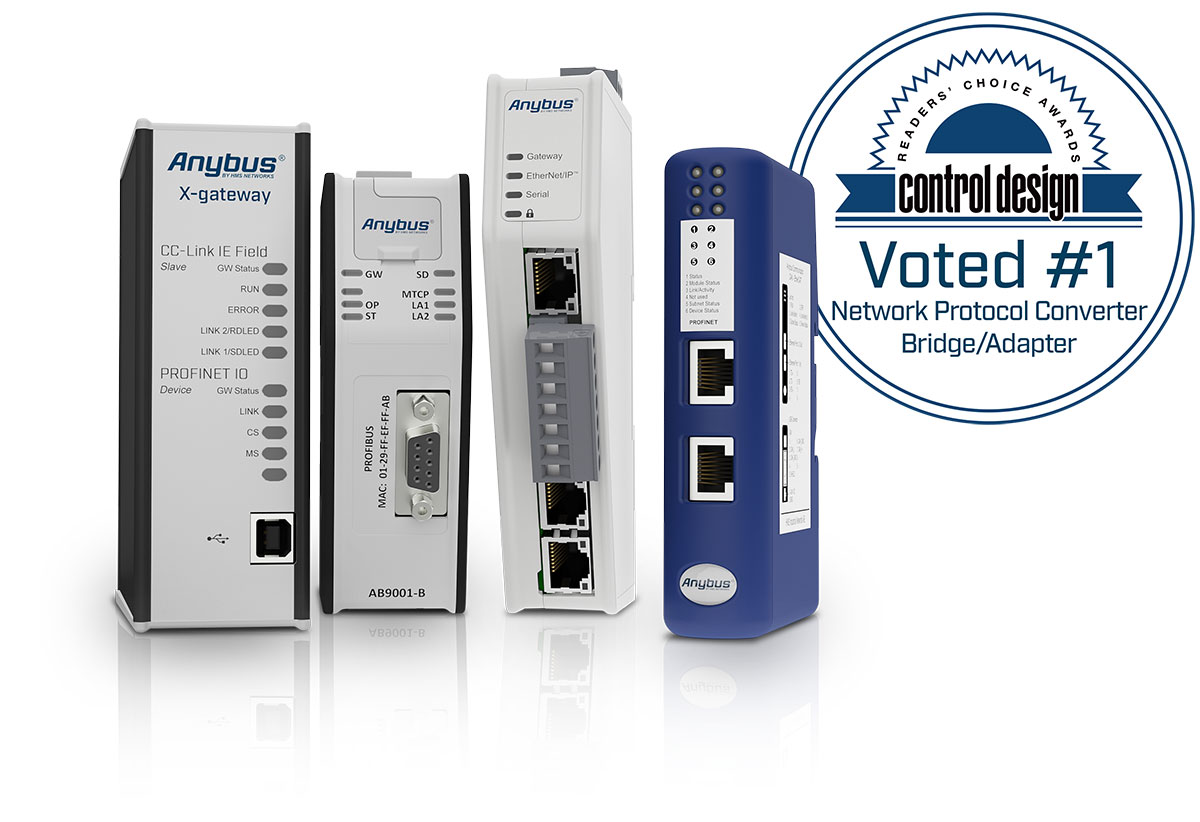
What Is a Communications Gateway?
An industrial gateway receives data from a variety of networks with various protocols and then converts the data to an understandable format that another network can identify. This data is then transmitted to other devices and networks or used internally in the PLC, HMI, or IPC. Other networks may be the edge data center or the cloud, where the data can be analyzed as required. The industrial gateway can include rate converters, signal converters, impedance matching devices, protocol converters, or fault isolators to assist with various network interfacing.Do I Need To Use an Ethernet Switch/Router Rated for Industrial Communications?
When deciding which type of switch to use, there are benefits to choosing an industrial-rated Ethernet switch. The major reason is that commercial switches can drop packets or pieces of data. Industrial network switches require high reliability where packet transfer is critical and dropped packets result in lost data. Commercial switches may not work at all with certain devices. You can set up industrial Ethernet switches in ring configurations that provide redundancy in the network and resilience in the automation system. The ring allows multiple transmission paths for the data.
Choosing between an industrial-rated Ethernet or a commercial switch comes down to application and operational requirements. Industrial Ethernet switches are designed for harsher operating conditions and more complex system programming. Industrial Ethernet switches are specifically designed for use in industrial plant environments, and they often exceed the specifications of the equipment connected to them. Industrial switches are installed in durable steel enclosures, whereas commercial switches cannot be mounted in this way as effectively. Another benefit is that industrial switches usually require DC power and have extra power inputs available, enabling the power supply to have a useable backup in case of a power failure. Some switch specifications such as shock and vibration are not defined in a commercial capacity but for industrial use. Some industrial switches can be installed and safely used in hazardous gas environments as they have a Class 1 Division 2, group ABCD rating. Commercial switches do not have this rating.
Contact the team at Applied Industrial Controls, Inc. today, and we will help coordinate your entire communications network.

MANUFACTURERS CERTIFICATIONS
