Are you starting an automation project that requires advanced knowledge and quality hardware? We have a range of solutions that will enable you to save time and coordinate devices seamlessly to ensure operational efficiency. Whether it’s Programmable Logic Controls (PLC) for industrial settings, Programmable Relays, Industrial PCs (IPCs), or Programmable Automation Controllers (PACs), we have the solution and support you need. Get in touch with us today to learn more about how we can make a difference in your project.
What Is
a PLC?
Your Options for Controls: PLCs
vs. PACs vs. IPCs
Why Should I Use Siemens
TIA Portal To Program PLCs?
What Are the Types of
PLC Programming Languages?
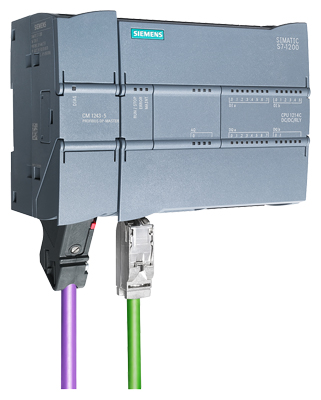
What Is a PLC?
A PLC, or programmable logic controller, is a piece of equipment that is designed to perform control functions in an industrial setting. PLCs are at the heart of almost all industrial and manufacturing processes and were developed to take the place of older relay logic. They are essentially powerful computers for industrial use. PLCs can be programmed and reprogrammed with algorithms which take the place of the physical wiring in older relay-based systems. Most are modular, which allows the addition of multiple functions and expansion over time, such as:- High-Speeded Networking
- Serial Communication
- Proportional Integral Derivative Control (PID)
- Motor Control
- Position Control
- Central Processing Unit
- Input / Output Cards or Modules
- Master module that the I/O modules are attached to
- Optional Power Supply Module
- Optional Communications Cards
- Optional Specialized Cards such as servo controls or specialized sensor modules
Should I Choose PLCs vs. PACs vs. IPCs?
If you're trying to decide between a PLC, PAC, or IPC, there are important factors to consider, such as system complexity and future operations expansion. Applied Industrial Controls, Inc. has subject matter experts in systems integration who can support your needs and questions.
In terms of controls, a PLC (Programmable Logic Controller) is an efficient, dependable, and cost-effective controller for small operations. It is the simplest to program and has a shallower learning curve than other automation controllers. In industrial settings, PLCs are usually connected with an HMI. There is a limit to the amount of logic that can be programmed into a PLC, as well as the amount of I/O capability; however, multiple PLCs can be networked together or expanded using optional control modules.
A PAC (Programmable Automation Controller) is a controller used for larger, more complex, and specialized operations where more processor power and memory are needed. These have all the capabilities of a PLC in addition to more advanced logic programming. PACs are often the most costly controller option and have a steeper learning curve than PLCs.
An IPC (Industrial PC) can handle the most complex operations while having the most flexibility. Programming is similar to conventional computer programming but is more complex; therefore, an IPC has the steepest learning curve. The controller is basically operated with a Personal Computer Platform that is highly industrialized and has more stable operating systems.
They have modernized processors and more memory than a PLC. A cost saving advantage of an IPC is that it can operate an HMI program on the same equipment as the automation program. This system is a Panel IPC or Panel PC where a touch screen is integrated with the IPC, making an all-in-one unit.
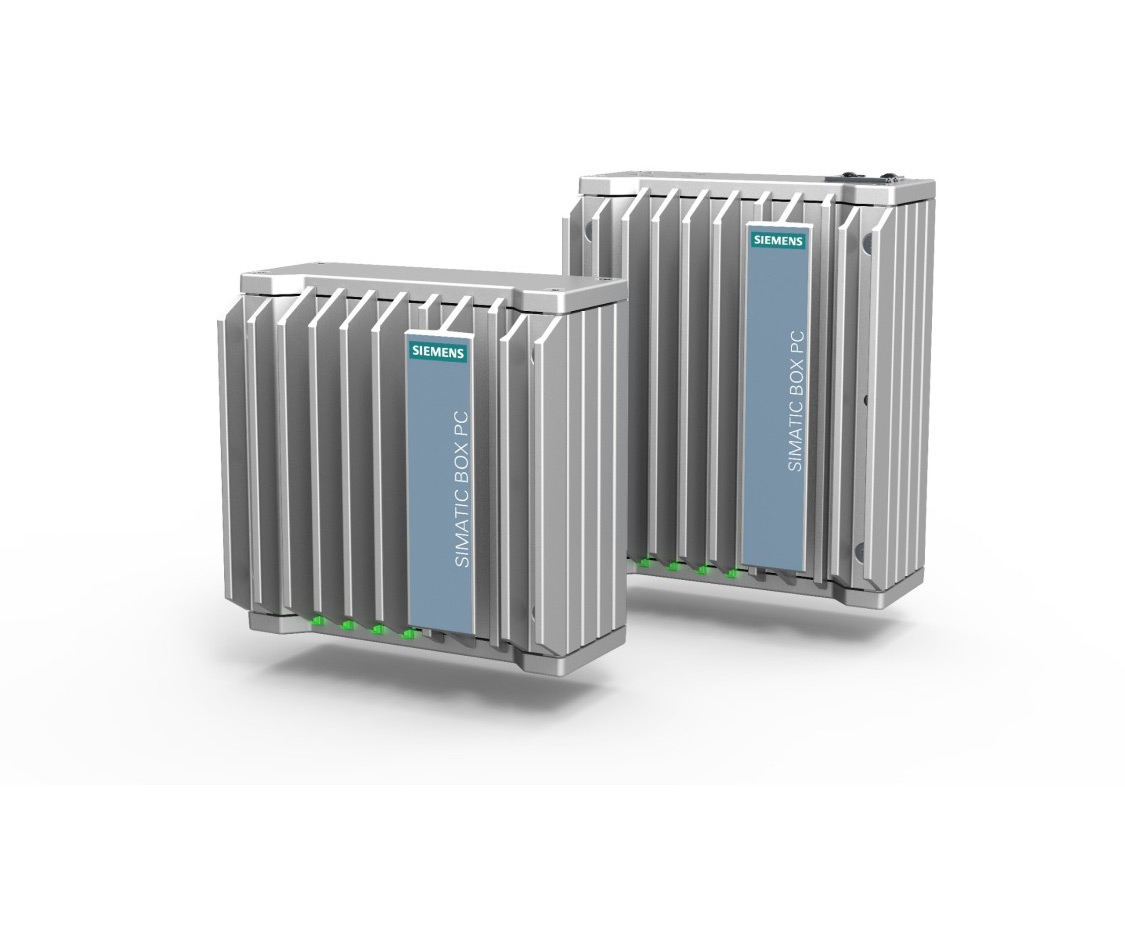
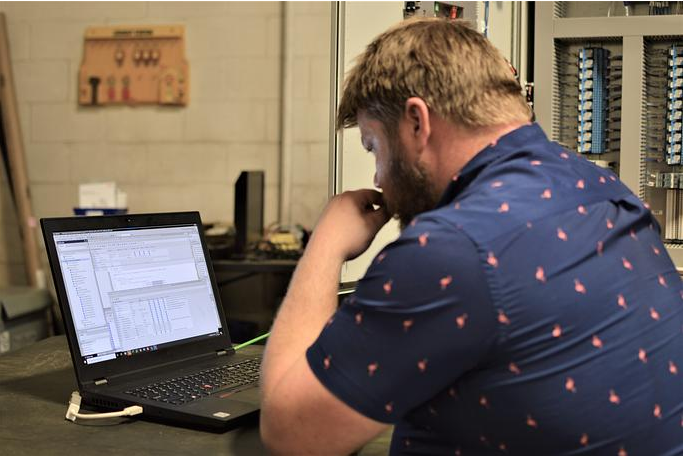
Why Should I Use Siemens TIA Portal To Program PLCs?
When it comes to programming PLCs, we recommend using Siemens Totally Integrated Automation Portal (TIA). This portal will allow you to manage a complete network of automation devices efficiently and easily on a single platform. Some of these automation devices include PLCs, VFDs, HMIs, CPDs, Sensors, Relays, Pilot Devices, and Power Supplies.
The TIA Portal gives a user unrestricted access to a library of digital automation services, simulation tools, additional diagnostics, and energy management tools. Implementing the TIA Portal in your business will enable effective automation of equipment, improved streamlined operations, and explicit communications with others in the organization.
What Are the Types of PLC Programming Languages?
There are five types of PLC programming language. Each has its own advantages that enable effective problem solving for many different applications. The TIA Portal mentioned above can handle either of the programming languages. This means that anyone, regardless of their proficient programming language, can program automation devices through the TIA Portal:
- Ladder Diagram (LD) – Uses digital circuits within a software platform and a microprocessor where logic is programmed into the software.
- Sequential Function Charts (SFC) – Use steps and transitions to perform operations. Steps contain programmed actions, and transitions contain data that is used for functions to move from one step to another.
- Function Block Diagram (FBD) – Uses function blocks between input and output that are linked with connection lines.
- Structured Text (ST) – Uses characters to program logic. It is a robust programming language that is capable of executing complex operations by using text functions, algorithms, and mathematical functions.
- Instruction Lists (IL) – This also uses characters to perform logic. These contain a list of instructions. Each instruction line contains data for specific operations and has comments included at the end of each line.
If you want industry-leading solutions and support for automation hardware, get in touch with the team at Applied Industrial Controls, Inc. today.
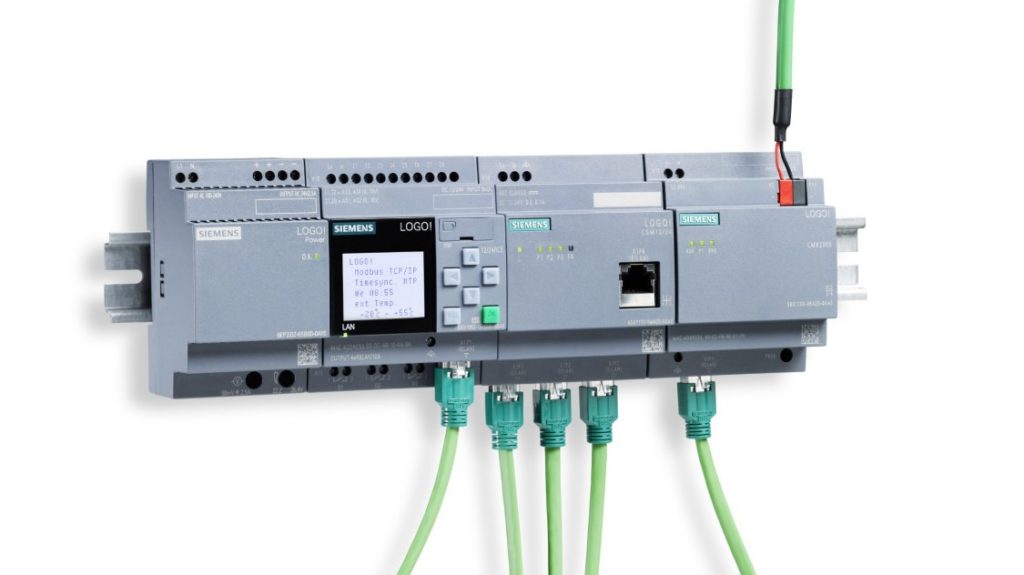
MANUFACTURERS CERTIFICATIONS
