How do you want your operators to interact with and run your equipment? With a high-quality HMI in place, you can consolidate user interaction to a single location to save time and reduce costs by eliminating wiring, reducing labor costs, and eliminating instrumentation like push buttons, indicator lights, and other pilot devices. Get in touch with us at Applied Industrial Controls, Inc. today to learn more about our HMI touch screen displays.
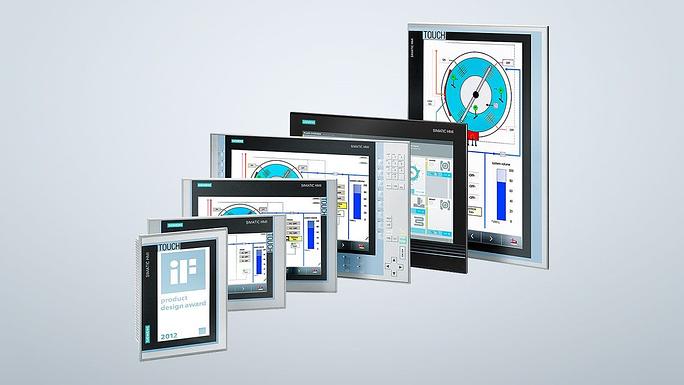
What Is an HMI/Touchscreen?
An HMI, or human machine interface, is a piece of equipment that allows communication between a person and the internal operations of another piece of equipment or a complete system of equipment working together. The interface is a visual and interactive touchscreen display that allows users to interact with the control system. The technology in the HMI is highly industrialized, increasing the durability of the component compared to a tablet PC or an iPad. Other terms for an HMI are MMI (Man-Machine Interface), LOI (Local Operator Interface), OIT (Operator Interface Terminal), and OT (Operator Terminal). However, most of those terms also refer to pilot devices such as physical push buttons and pilot lights. Some common uses for an HMI in industrial settings are:- System controls and operation
- Alarm and fault notification and reset
- Maintaining and collecting key performance indicatory (KPI) programs and logging data
- Monitoring inputs and outputs of data from equipment
- Visually displaying system and equipment data for human monitoring
- Tracking production data such as production time, quality control, and production trends
Should I Choose an HMI Touch Screen Display or Panel IPC?
HMIs have many common uses in industrial process control. Some of these include monitoring and storing sensor inputs, visually displaying real-time equipment and system data, notifying of new or abnormal changing data by sending messages, initiating alarms, remotely controlling equipment and machines such as starting and stopping, and sharing and sending data efficiently.
HMIs are complex, compact, and have no moving parts. If an HMI touch screen display experiences a failure, another HMI with the exact configuration is required to replace the failed HMI without disrupting production.
An alternative to an HMI is a panel IPC or Industrial PC. These can be the preferred process control units because of increased capacity and data processing capabilities. They can store critical data locally, whereas HMIs and PLC Process Control Devices have more limited storage capacities. An Industrial PC operates with a Personal Computer Platform that is highly industrialized and has a more stable operating system. They have modernized processors and more memory than a PLC. A cost saving advantage of a panel IPC is that it can operate an HMI program on the same equipment as the automation program. This system is a Panel IPC or Panel PC where a touch screen is integrated with the IPC, making an all-in-one unit. The programming of a panel IPC is typically more complex than an HMI and PLC; however, the IPC has more capability for complex data analysis. HMIs and PLCs have more expandability for growth and additional integrations.
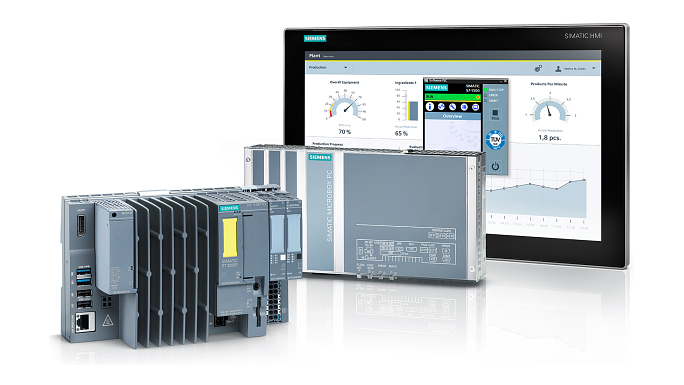
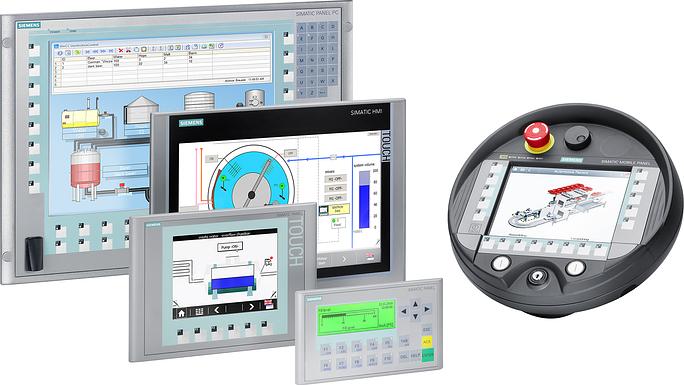
Why Go From Physical Buttons to an HMI?
Even though physical buttons have been commonplace in industrial processes for decades, switching your operator interaction from physical buttons has many advantages that will simplify and modernize your operations:
Large, Detailed, and Professional Screens – HMIs provide clear graphics that reduce errors in data interpretation and control decisions. Graphics can include actual equipment diagrams or pictures of the physical equipment and operations.
User-Friendly Controls – It is convenient, efficient, and safe to have real-time operational data from a centrally located process. On HMIs, it is simple to change the operational status of a piece of equipment by selecting commands on a touch screen device. Images of the equipment can be displayed on the screen, so the user knows the exact function of the virtual button rather than the abstract function of a physical button.
Enhanced Security – Security levels can be created on HMIs to limit the number of people who can access certain data and controls.
Broad Functionally – Required data can be presented logically and for any time in history on graphical touchscreen displays.
Greater Flexibility – Features can be added or controls reconfigured for little to no cost. This can combine and standardize production lines or provide system upgrades without significant changes to the industrial control panel.
Financial Savings – Converting an industrial control panel from physical switches and controls to an HMI will save money through reduced labor and component costs.
What Should I Consider When Choosing an HMI?
There are many considerations when choosing an HMI to control your operations. The team at Applied Industrial Controls, Inc. will work with you to find the ideal solution for your monitoring and control needs. Some critical considerations are:
Site Conditions – Things like temperature, water and chemical exposure, and vibration will determine if special casings are required to keep the HMI protected.
Data Monitoring Requirements – Knowing what data is essential to be communicated and monitored will determine the complexity of the HMI.
Screen Size – The amount of data required to be displayed will determine the type, resolution, and size of the screen that will best suit the application.
The HMI Provider and Level of Support – Having a provider that can support newer and older devices and provide timely, knowledgeable, onsite support is a benefit that not all providers offer.
Additional features to consider in an HMI are:
- Built-in web server and remote access
- User access security control
- Simple user interface
- Data Management
- Programmable alarms
- Multimedia support
- Backlight display
- Capacity for future expandability
- Development templates
Get in touch with AIC today, and we will help find the most logical HMI that meets your needs and budget.
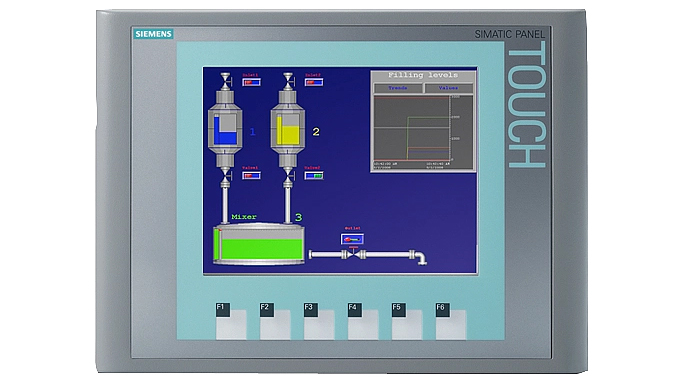
MANUFACTURERS CERTIFICATIONS
